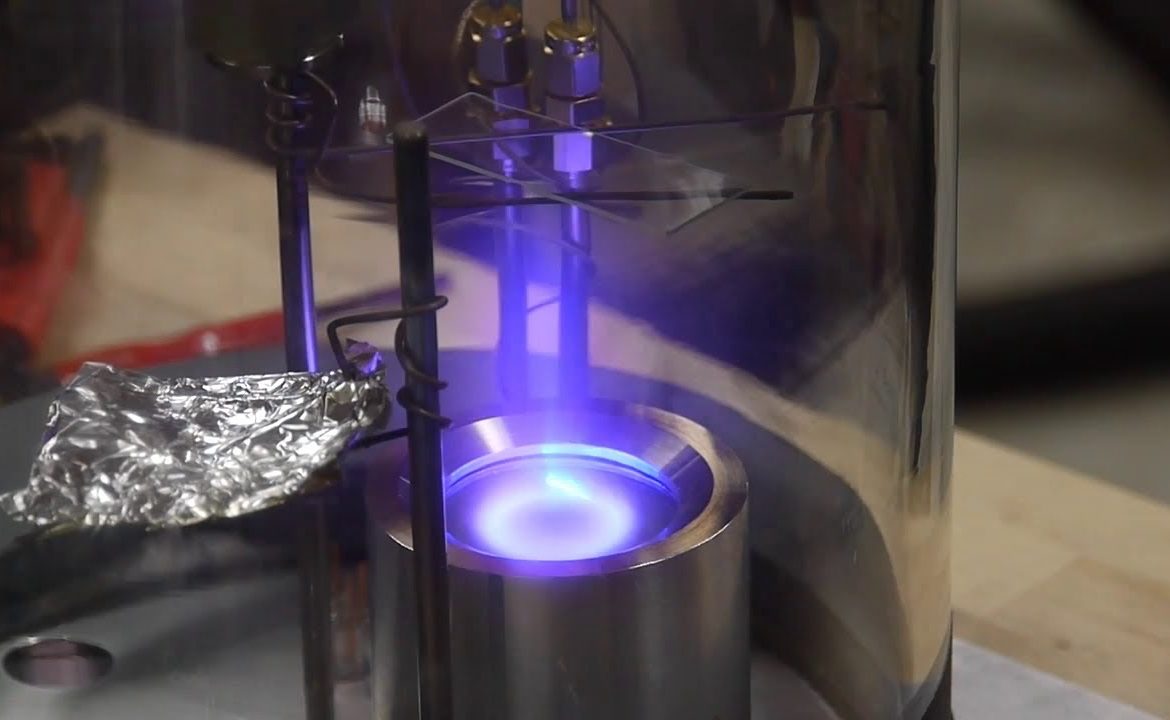
The first topic in the headline is self-explanatory but the second? If we take a look at sputter coating, its history, and its advantages and disadvantages, we would be hard pressed to understand why it is not the leading technology for coating lenses. Let’s look at the facts, follow the introduction of the RFX-10 in the US and decipher what actually killed sputter.
Sputter coating on a global scale is probably the most accepted method for thin film applications. Precision Optics, Semiconductor Applications, Fine Optics, Laser Coatings and many others are done with this method. When we look at the advantages of this technology closely, we can see why.
- High deposition rates
- High yields
- Low relative temperature
- High molecular energy
- Cheaper vacuum systems
- Robust coatings
- Uniformity
- Stability
- Short cycle times
If all of these things are true (you can look all of this information up easily on Wikipedia or other methods), why did sputter (there are many types but traditionally magnetron, pulsed DC, reactive gas is the preferred method) technology fail in ophthalmics?
What most people remember, or at least have heard stories of, is the introduction of the RFX-10 into the US market. The program failed. But why did it fail? I would argue for some of the same reasons that the ion source and ion assisted deposition almost failed in the US. We didn’t know how to use it properly and we didn’t understand the importance of hardcoating under the AR as well as we should have.
The value of hardcoating was taught early in my career (by Russ Custer) with the analogy of the sponge, piece of wood and a microscope slide. If you put the microscope slide on top of a sponge and push, the slide will break. If you put a small piece of wood in between the slide and the sponge, you can push as much as you want and the sponge will flex but the slide stays in tact. In this analogy, the sponge is a lens. The microscope slide represents the AR coating and the wood represents a hardcoat. The thickness, flexibility and relative hardness are a good fit for the items they represent.
When the RFX-10 was introduced, Poly wasn’t really established, CR-39 was predominant, glass was still widely used and dip hardcoating was nonexistent (except for manufacturers). I am not sure about the market penetration of backside spin coating. But, I do know that a lot of lenses were uncoated CR-39 or semi-finished CR-39. I would argue that Zeiss gained a great foothold in the US because their AR had very good adhesion to unhardcoated lenses. Frequently, there were difficulties in producing a successful AR coating on these lenses. There was a very strong education program to get the market to understand that the lenses had to be hardcoated to be successful with AR coating.
Because sputter coating has higher molecular energy than EB gun evaporation, the density of the coating is higher. This leads to a harder AR coating (in most cases), which is good IF there is a good hardcoat on the lens.
The market is now ready for the reintroduction of this stable and robust technology. There are several out there now. Satis has the SP-200 and Quantum has the Fusion line of systems.
Their sputter types differ somewhat but when you look at what these small systems are capable of, you will quickly be in awe. The Fusion for example has a throughput time of a lens every 3 minutes (average) for ANY coating. This lends the system to true linear manufacturing and the elimination forever of the BATCH. But that discussion is for another time.
Sputter’s time has come and this technology will change vacuum coating in Ophthalmics forever. Hardcoating may have killed this technology in the past but with the wide use of hardcoats, even dip hardcoats, and Polycarbonate (the ideal lens for hard AR coatings) Sputter will be much more successful now. Just ask the folks at Lens Crafters….
Follow Norm Kester on LinkedIn or on Twitter @opticalcoatings.