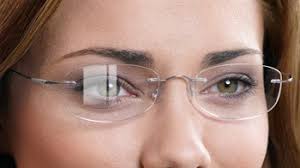
I have had many conversations through the years regarding Cracking and Crazing of AR coating, and what causes each. In this article, I want to discuss several of the things that lead to Cracking and Crazing in an effort to understand the relationship between the lens, the layers of the coating and the coating as a whole.
The Lens
One of the most important things to understand related to this topic is that lenses have what is scientifically referred to as a coefficient of thermal expansion. This is a fancy way of saying that the lenses expand and contract with temperature. When the lens expands and contracts at a different rate than the AR coating, the AR coating can, and very often will, crack. (Keep in mind the AR coating is very, very thin relative to the lens.) The highest coefficient of thermal expansion in lenses belongs to Hi Index, then CR39 and Mid Index. Poly and Trivex have relatively little thermal expansion. If we are going to see temperature related cracking, we will typically see it first in Hi Index and then follow it down. One hardly ever sees temperature related cracking in Poly.
The Layers
The applied films, or materials, that make up the AR coating have what are called “intrinsic stresses”. This means that the materials, by their very nature, have stress in them. For instance, Silicon Dioxide, which is a major component of most ophthalmic AR coatings, has intrinsic compressive stress and Titanium Dioxide and Zirconium Dioxide, two more major components of AR coatings have intrinsic tensile stress. Compressive (concave) stress is curling toward the lens and tensile (convex) stress is pulling away from the lens.
Cracking Related to Stress
When a film has too much compressive stress relative to adhesive strength, it buckles up and delaminates from the lens in lines. This would be similar to what you typically see in an earthquake scene in a movie. The stress causes the coating to buckle up. That pressure exceeds the adhesive strength of the coating to the lens and the coating breaks or cracks at the highest point of stress.
Crazing Related to Stress
When a film has too much tensile stress relative to its cohesive strength, a number of fine cracks form to relieve the stress. The fine cracks will appear and be joined at right angles to one another. When the coating does this, it is said to be crazed. The coating is pulling away from itself in this case. Here is a view of a film in tensile failure or crazing.
What Can Be Done?
To solve these issues, first understand the limitations of the coating/lens combination. If you are choosing to AR coat a lens with a high coefficient of thermal expansion, don’t put an AR coating on it that has a high level of stress (usually a coating with high scratch resistance). Choosing a coating with less stress is a good choice, or put a better buffer (dip hardcoat) between the AR coating and the lens.
Second, understand your AR coating. You need to know if your AR coating is well balanced in the area of stress. To understand this well, see how your AR coating does in a thermal shock test. I would suggest applying your AR coating on a Sola CR39 -2.00 lens and putting it through the test. If your AR coating can make it through the test with a 4 or 5 rating, you have an extremely well balanced AR coating. If you need help balancing your AR coating stack or choosing a better one, contact your AR coating provider or us here at Quantum.
Follow Norm Kester on LinkedInor on Twitter @opticalcoatings.